ほとんどの浮上分離装置は、あまりうまくいっていません
浮上分離用のマイクロバブルは、「できます」とPRしている会社は多くありますが、本当の意味で良く出来ている、という現場は非常に数少ないのが実情です。つまり、実際にはあまりうまくいっていないのが浮上分離と言えます。
圧倒的に普及しているマイクロバブル生成方式は【圧力タンク方式】ですが、圧力タンクの調整は非常に厄介で、
いつのまにかマイクロバブルがまったく出来なくなっていたりします。
なぜ、圧力タンク方式はうまくいかないのか
エアーはそう簡単には、理論通りに溶けません
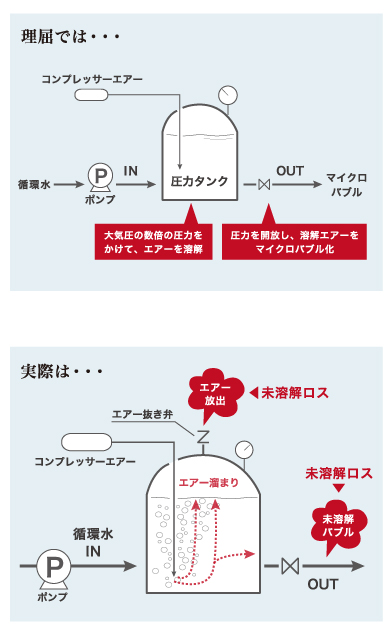
「ヘンリーの法則」として知られているとおり、大気圧の2倍の圧力をかければ2倍のエアーが水に溶け、5倍の圧力をかければ5倍のエアーが水に溶けます。
これを応用したのが「圧力タンク方式」で、大気圧の数倍の圧力でエアーを水に溶かし、それを大気圧の下に解放することで溶存エアーが溶けていられなくなり、マイクロバブル化する、という仕組みです。
しかし圧力タンク方式では、理論通りにエアーは溶けません。
理由は、コンプレッサーエアーが水中で吐き出された瞬間に、そのほとんどが粗大バブルになって水と瞬く間に分離してしまい、未溶解のエアーが大量に発生してしまうからです。
未溶解のエアーは圧力タンク上部の「エアー抜き弁」や「圧力タンクの出口」から吐き出されます。
(※右のイラストをご覧ください)
「圧力タンク方式」の技術的な最大の欠陥は、ここにあります。
つまり、吹き込んだエアーのうち実際にどれくらいが溶解して、どれくらいが分離するのかが正確に判らないという点です。
たとえ吹き込みエアー量を増やしても、粗大バブルが増えるだけでマイクロバブルは増えない、ということも起こります。
さらに、日々の微妙な圧力タンクの内圧の変化でも、溶解・未溶解の割合は変化してしまいます。
よって、最適な運転条件を見出すことが非常に難しく、いつの間にかマイクロバブルが生成出来なくなる、といったことが起きてしまうのです。
OHR式は、マイクロバブル生成メカニズムがまるっきり違います
圧力に頼らない エアーの離脱がほとんどない 運転調整が非常に簡単
OHR式浮上分離のメリットは、加圧タンク方式と違って初回の調整だけで済み、その後は《長期にわたる安定運転ができる》《日々の微調整はまったく必要なくなる》ということです。
他に例をみない大量処理も得意です。
機器構成は、OHRミキサーとポンプだけで、とてもシンプルです。図解にまとめてありますので、詳細はお問合せ下さい。
マイクロバブルの細かさも、群を抜いています
某水処理会社による、国内メーカー3社の比較試験結果
某水処理会社が、国内マイクロバブルメーカー3社のマイクロバブルの細かさを比較テストしました。
各社の装置で生成したマイクロバブル水を1ℓメスシリンダーに採り、マイクロバブルの持続時間を測る、というものです。
他社は75秒、90秒であったのに対して、OHR式は170秒でした。
(※このレポートは呈上いたします)
「浮上分離」においては、白濁したマイクロバブルが微細であればあるほど、SS(懸濁物質)に絡み付いて上昇させる力があります。
同じ「マイクロバブル」といっても、SSを浮上させ、分離させる能力に大きな差があるということです。
既設の浮上分離装置の性能改善事例が、次々に増えています
某製紙工場では、1月あたり100万円もの凝集剤(=薬品)が削減できました
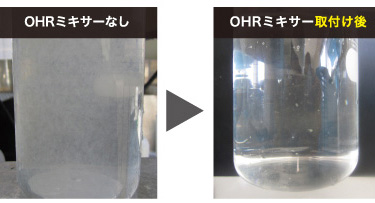
某製紙工場では、古紙繊維の回収・再利用のために、浮上分離装置を使っている。繊維長は0.1~0.3mm、SS濃度は100mg/ℓと非常に少量・微細であるため、充分に回収できず、大量の古紙繊維が処理水中に流出し、後処理工程の濾過器が頻繁に目詰りしていた。(写真左参照)
OHRミキサー取付け後はマイクロバブルの出来が良くなり、浮上分離槽内での古紙繊維の回収率がアップしたため、 濾過器のフィルターの逆洗時間が、3時間おきから8時間おきに、大幅に延びた。(写真右参照)
【途中の配管を切断してOHRミキサーを挟み込む】だけで、マイクロバブルの出来具合を改善し、浮上分離性能を劇的に改善できます。
マイクロバブルの出来具合が悪いと、凝集剤に頼った浮上分離となり、薬剤の使用量は増えます。つまり、マイクロバブルの出来具合を劇的に改善すれば、自ずと凝集剤の使用量も激減します。
某製紙工場では、1ヶ月あたり100万円もの凝集剤を削減できました。
レンタル用OHRミキサーを、今お使いの浮上分離装置に実際に取付けてみて、凝集剤削減効果をご確認ください。
導入の価値があればお買い上げ頂きまして、購入する価値が無ければ返却頂く、という、もっとも公平なやり方です。