液−液抽出法 (溶媒抽出法) における、油−水の弱混合
OHRミキサーは流体を微細に砕く能力が非常に高いため、数ミクロン〜ナノオーダーの粒子径が要求される用途に使われることが多いですが、ここでは少し変わった使われ方をご紹介します。弱く、かつ均一に混合するテーマです。
「液液抽出法 (Liquid–liquid Extraction) とか「溶媒抽出法 (Solvent Extraction Method)」という、液中から狙った物質だけを選択的に取り出す手法があります。水と油が互いに混じり合わない性質を利用し、主に金属製錬や食用油精製、香料の抽出などの分野で用いられます。
ここでは銅の製錬を湿式でおこなうケースを例に、そのプロセスを簡単にご説明します。
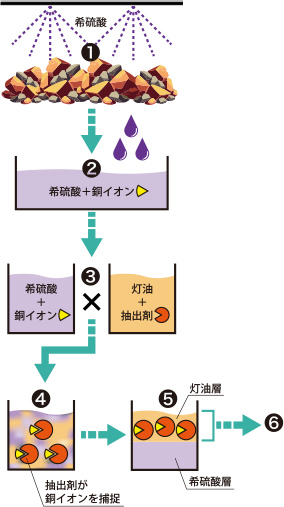
❶銅鉱石(粉体)や銅スクラップを、希硫酸と接触させる(噴霧するor浸す)
❷希硫酸に銅イオンが溶け出す
❸撹拌機で、灯油と混合する。
灯油にはあらかじめ、銅イオンだけを選択的に捕捉する抽出剤を溶かしておく。
❹希硫酸(水相)に溶けていた銅イオンが、灯油中の抽出剤にキャッチされて
灯油(油相)へと移動する
❺希硫酸(水相)と灯油(油相)が2層に分離するまで静置する
❻灯油(油相)を次の電解採取工程に回し、銅を得る
液−液抽出法が抱える課題
液−液抽出法は、「混ぜる」と「分離」を両立させたい、という矛盾を抱え込んだ手法です。
上記のプロセス❸❹では、油−水が互いに細かく入り混じることで、水相と油相との間で物質移動が進む。しかしプロセス❺では、油−水をきれいに分離させることで、目的物質の回収が進む。
「混合」と「分離」のどちらもうまくいかないと、収率が悪くなってしまいます。この相反する2つをバランス良く両立させるためにOHRミキサーが役立つことを、これから順を追ってご説明します。
液−液抽出法における油−水の混合には撹拌機が多く使われますが、そのメカニズム上、ほどよく接触させるのがとても困難だという厄介な課題をかかえています。
撹拌機は撹拌翼を回転させて油−水の混合・接触を図りますが、生み出される液滴サイズの分布が不均一であるため、以下の問題が生じます。
- 目的物質の相間移動にムラが生じる
- 油−水を接触させたあとの分離工程で、微細になりすぎた液滴は分離効率が悪く、収率悪化につながる
- 分離しきれなかった油滴が水相に残って汚濁させてしまうと、その入れ替えや廃棄の手間やコストの負担が増す
つまり油滴サイズが細かすぎても、大きすぎても、収率は悪くなります。
ここで、撹拌機の作動メカニズムに焦点を当ててみます。 撹拌機の回転翼は、軸芯から近い・遠いの差がある分、微細化作用を比較的強く受ける部分と弱く受ける部分の差が生じるのが当然であり、液滴サイズの分布が幅広くなるのはやむを得ません。 そしてまた、回転する撹拌翼が当たらず逃げてしまう油−水が一定量残ってしまいます。
1つ目に、液滴サイズの分布がブロード(幅広)であってシャープでない。
2つ目に、撹拌翼から逃げてしまう部分が残る。
2つの意味で「原理的限界」をかかえているのが撹拌機だといえます。
OHRミキサーが使われた実績例
OHRミキサーが有機溶剤の抽出に使われた実績をご紹介します。
- 排水に、3種の有機溶剤が含まれています。トルエン、シクロヘキサノン、シクロヘキサノンオキシムの3種です。濃度は3つとも、200ppm前後という低濃度です。
- この排水にたいし、トルエンを混ぜることによって後者の2つ、つまりシクロヘキサノンとシクロヘキサノンオキシムとを分離抽出するのが目的でした。(トルエンは純粋品ではなく、すでに抽出に使用したあとのリサイクル品)
- 排水+トルエンをOHRミキサーに通した圧力は、わずか0.03MPaでした。(一般家庭の水道圧のおよそ1/10の低圧)
- 結果、いずれの有機溶剤も高効率で回収でき、非常に高い評価を得ました。
シクロヘキサノン ⇒ 理論抽出率の96.1%
シクロヘキサノンオキシム ⇒ 理論抽出率の91.0%
この内容を記したレポートは呈上できます。よろしければお求めください。
お問合せ
OHRミキサーを液−液抽出法に使う場合の、基本的なやり方
OHRミキサーを使うと、狙い目ゾーンにちょうどよい油−水の接触ができます。ポイントは、【少量&低圧】で油−水をOHRミキサーに流し入れることです。(注:【多量&高圧】で流し入れると、粒子サイズが微細になりすぎますので禁物です)
油−水がほどよく接触し、そのあとスムーズかつきれいに分離する最適な【流量&圧力】を見いだす事前テストが重要になります。(ポンプの流量&圧力をインバーターでコントロールし、最適条件を見い出す)
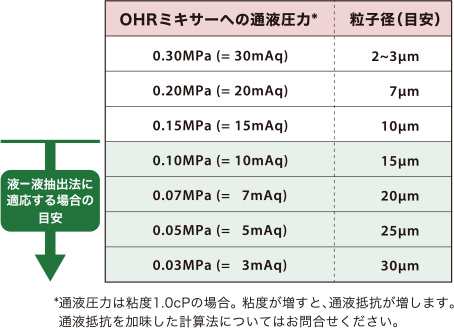
目安の圧力は、0.10MPaよりも低い圧力です。それが0.07MPaなのか、0.05MPaなのか、あるいは0.03MPaなのかは、試しテストで判明することです。
ご参考にお伝えしますと、OHRミキサーはわずか0.3MPaほどの圧力で、【軽油+水】を2〜3ミクロンの粒子サイズに乳化させます。しかも乳化剤(化学薬品)は添加せず、物理的な作用力だけによる乳化です。
したがってOHRミキサーを液−液抽出法に使う上で、0.3MPaという圧力では高圧すぎることは明らかです。
では、より低圧ではどれくらいの粒子サイズになるかといいますと、右の一覧表を目安にしてください。
OHRミキサーの比類なきメリット
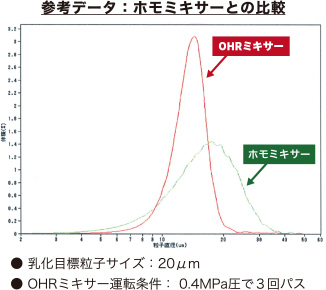
OHRミキサーを液−液抽出法に適用するメリットを5つ、ご紹介します。
第1のメリット:
液滴サイズの分布がシャープであることです。
ケーシングの内部で羽根を高速回転させる「ホモミキサー」と比較されたグラフを右に示します。
なおこのテストではOHRミキサーを複数回通しましたが、実際には1回だけ通すワンパス処理で使われることがほとんどです。
第2のメリット:
OHRミキサーへ流し込んだ油−水は、その全量がもれなく微細化作用を受けます。
撹拌機のように、微細化作用を受けない油−水が残ることがありません。
ポンプで流体をOHRミキサーに流し込むだけで、一瞬でもれなく、微細に砕かれ微粒子群に変貌します。下のメカニズム図でご理解ください。
第3のメリット:
OHRミキサーの内部構造は精密に組み上げられており、そこへ一定の流量と圧力で流体を流し込めば、狙った剪断力が常に作用し続けます。これはつまり、狙い目ゾーンにちょうどよい油−水の接触が非常に安定して達成できる、ということに他なりません。
第4のメリット:
OHRミキサーはただ単に、粒の揃った液滴をつくり出すのではありません。独自のメカニズムによって、水相から油相への物質移動を一瞬で完了させます。
OHRミキサー内には、強烈なヒネリを流体にたいし加える構造物「ガイドベーン」が仕掛けてあり、これによって強い遠心力がかかり、重質の流体粒子群は外側に、軽質の流体粒子群は内側に、一瞬で別々の層に分かれます。
そしてこの際、流体粒子群どうしが激しく衝突し合います。
そしてさらに「カレントカッター」による粒子群どうしの衝突が繰り返されます。
この2段階の流体粒子群の衝突の際に、水相から油相への物質移動が完了するわけです。
仮に、OHRミキサーによって30ミクロンほどの液滴サイズをつくり出すことがベストだと判明したとして、では他の装置で同じサイズの液滴をつくり出せば同じ抽出効率が得られるかというと、そうではありません。そこには、質的な違いがある。
「結果として30ミクロンの液滴サイズを生み出すだけのミキシングの強度が、OHR式を液−液抽出法に使う場合にはちょうどふさわしいのだ」という理解こそが正しいわけです。
そこで、たとえば従来考えられていた最適な粒子径より大きめであっても、OHR式であればより高効率の抽出が達成できる可能性が高いわけです。
第5のメリット:
OHRミキサー内部を流体が通過する時間は、わずか0.04秒です。OHRミキサーは、毎分あたり数千リットルの巨大量でも一瞬で油−水混合できますから、大幅な処理時間短縮が可能です。これまで撹拌機で混合のために割いていた時間のうちの短縮分を、分離工程の静置時間を延ばすことに活かせます。
有価物の分離を、より高速で、効率的におこなうために
廃棄されたリチウムイオン電池から、リチウム・コバルト・ニッケルなどのレアメタルを回収するというような場合に、液−液抽出法は現段階ではもっとも頼りになる技術といってよく、その役割はいっそう重要になっていくと考えられます。
ただ油−水の接触に撹拌機を使っているかぎり、収率の改善はさほど期待できないでしょう。先述のとおり「原理的な限界」を抱えているからです。
たとえば約30ミクロンの液滴サイズにそろえると、混合にも分離にも、ちょうどよいのだと判明したら、その液滴サイズを精確につくり出す技術でないといけない。しかも、長期にわたる安定運転ができないといけない。
この要請に応えられるのは、OHRミキサーが随一だと思われます。