OHR MIXER
DAF / Micro-nano bubbles / Emulsification / Uniform dispersion / Ozone treatment / Neutralization & pH control / Others
OHR AERATOR
Air diffuser for wastewater treatment / Prevention of sludge accumulation / VOC removal, Degassing / Gas-Liquid reaction
Limitations of conventional technology |
OHR technology |
Pressure tanks require burdensome daily pressure adjustments, as well as periodic replacement. |
Does not use a pressure tank at all. Once initial setup is complete, absolutely no further adjustment is required. |
Requires both a high-pressure pump and high-pressure air. |
Injects air at an exceedingly low pressure of 0.1 MPa. Pump has the same power rating as a standard water pump. |
Relies on large amounts of flocculant to remove SS because its poor-quality microbubbles cannot. |
Generates high-quality microbubbles with exceptional consistency. Cuts flocculant usage by 20–30% in most cases, and up to 50% in some cases. |
Large-scale treatment operations require multiple units, installation of which is complex and cumbersome. |
Generates up to 15,000 L/min of microbubbled water with a simple combination of one OHR MIXER and one pump. Operates with minimal pump power and piping. |
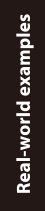 |
- Generating large amounts (1,800 L/min) of microbubbled water with an OHR MIXER MX-F80 and a 22 kW pump.

- Flocculant-free flotation and separation of SS and FOG (fat, oil and grease) in wastewater containing oil.
- Numerous examples in which installing a single OHR MIXER into an existing DAF system markedly improved its separation ability.

|
Limitations of conventional technology |
OHR technology |
Most are capable only of producing tiny quantities, which are suitable only for laboratory tests or small-scale plants. |
Capable of generating anywhere from 10 L/min up to an enormous 15,000 L/min. Can handle both large-scale wastewater treatment facilities and large-scale chemical plants. |
Only a limited number of gases can be turned into micro- and nano-bubbles. Some technologies cannot produce such bubbles in pure water. |
Breaks down gases and liquids into micro- and nano-particles irrespective of their type. |
Equipment is complex. Uses a pressure tank or a high-pressure pump. Some technologies can only generate these bubbles in a container of water. |
Consistently generates micro- and nano-bubbles with the simple combination of an OHR MIXER and pump. |
Most equipment is only capable of generating one type of bubble, e.g. only microbubbles or only nanobubbles. |
Simply operate a valve to switch between microbubbles, nanobubbles and coarse bubbles as required. |
Merely uses differences in pressure to generate micro- and nano-bubbles. Contact and reaction between the liquids and gases is left entirely to chance. |
Generates bubbles at the same time as the gas and liquid make contact and react inside. Being a reactor, not merely a bubble generator, a single OHR MIXER can replace conventional reaction equipment. |
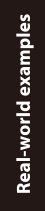 |
- Rapid, efficient generation of nitrogen micro- and nano-bubbles for use in deoxygenation via the nitrogen substitution method.

- Reacting organic solvents and CO₂ gas.
Reaction times have fallen from 11 hours to 6–7 hours and CO₂ usage has fallen by almost 50%.
- Ozone treatment to decolor 5,000 m³/day of colored wastewater at a paper mill, without the need for a waste ozone destructor.
- Producing urethane sponges with finer and more numerous pores.
|
Limitations of conventional technology |
OHR technology |
Requires very high pressure to emulsify without the addition of chemical emulsifier. |
Capable of emulsifying water and light fuel oil without emulsifier, in a single pass, at a pump pressure of just 0.3 MPa. |
Requires bulky, complex and expensive emulsification equipment. |
Just one OHR MIXER and pump can replace high-pressure emulsification equipment. |
Requires regular maintenance and replacement of parts, making it impractical or impossible to use in areas where such support is unavailable. |
No moving parts, no replacement parts, no consumable parts. The OHR MIXER is completely maintenance-free. |
Requires a large amount of emulsification equipment to make large amounts of emulsion because each unit can only process a limited amount. |
Can process up to 15,000 L/min with one OHR MIXER and one pump. |
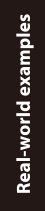 |
- High-pressure emulsification equipment costing in excess of $200,000 was replaced with an OHR MIXER that costs a mere $3,800 and runs at 1/100 the pressure.

- Producing pork bone broth (emulsion) in large quantities and at speed.
- More than 300 other past successes.
|
Limitations of conventional technology |
OHR technology |
Stirs in a large tank, using the blades of an agitator. Continues until uniform dispersion is achieved. |
Instantaneous uniform dispersion in a single pass. Simply send both fluids through the OHR MIXER. |
Mixing takes time and requires bulky, complicated, expensive equipment. |
Can achieve uniform dispersion in just 0.04 seconds with the simple combination of one OHR MIXER and one pump. |
Regular disassembly and cleaning is both time- and labor-intensive, owing to the large number of component parts. |
Self-cleans. In the majority of cases, cleaning is as simple as sending through the cleaning solution. |
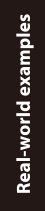 |
- Cooking oil producer N now uses OHR MIXERs at all of its facilities to mix in additives at an ultra-low concentration of 3.0 ppm (parts per million) in a single pass.

- Chemical company D uses OHR MIXERs to mix trace amounts of water into organic solvents. No mixing equipment proved capable until the OHR MIXER, which enabled uniform dispersion for the first time.
- Uniformly dispersing flavoring oils in viscous liquid.
- Food manufacturer R uses the OHR MIXER to uniformly disperse vitamin C powder in cooking oil.

|
Limitations of conventional technology |
OHR technology |
Draws wastewater into a large tank before bubbling ozone. Contact and reaction takes a much longer time. |
The entirety of the wastewater and ozone gas makes contact and reacts inside the OHR MIXER.  |
Releases large amounts of unreacted ozone gas, which requires an ozone destructor to break down. |
Releases virtually no ozone gas, making ozone treatment possible without ozone decomposition equipment. |
Requires a large reaction tank, large ozonizer, and ozone destructor. Extremely expensive. |
Allows all of the equipment to be made significantly more compact than with the conventional method. One particular factory was able to introduce an OHR-based ozone treatment system for a third of the cost. |
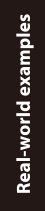 |
- Paper mill T uses OHR MIXERs to ozonize 5,000 m³/day of colored wastewater, without an ozone destructor.
- Successfully decomposing dioxins, which were widely supposed to be undecomposable using ozone alone.

- Complete deodorization of 3,000 Nm³/min of foul-smelling vent gas from an electric furnace. Achieved by spraying highly-concentrated ozonated water from an OHR MIXER.
|
Limitations of conventional technology |
OHR technology |
Attempts to achieve a desired pH level using a propeller agitator and a large tank, but is plagued by large, rapid fluctuations in pH caused by non-uniform mixing. |
Eliminates fluctuations in pH by mixing the liquid and pH-adjusting agents completely and uniformly within the OHR MIXER itself. |
Mixes pH-adjusting agents non-uniformly, resulting in variable, inaccurate pH readings and ultimately the under- or overaddition of adjusting agent. The desired pH is thus never achieved, and chemicals are wasted. |
Injected pH-adjusting agent is uniformly mixed the moment it passes through the OHR MIXER, eliminating waste. |
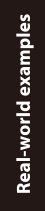 |
- Sugar producer M had been using caustic soda to neutralize wastewater that fluctuated rapidly between acid and alkali. Introducing the OHR MIXER eliminated these fluctuations and cut caustic soda usage by some 30%.

|
Other real-world uses of the OHR MIXER |
|
- Simultaneous oxidization and fine dispersion of pigments in organic solvents

- Demulsification by the application of extreme shear forces
- Circulatory mixing to preventing moisture in jet fuel from freezing during flight
- Artificial production of methane hydrate
- Instantaneous dilution of chemicals to an exact concentration
|

Limitations of conventional technology |
OHR technology |
Inevitably clogs, necessitating regular cleaning and replacement. |
Never clogs. Performs like new even after 15 years of use.
 |
Cannot install or replace without draining the tank. |
Can install without draining the tank.
 |
Markets itself as “high-efficiency”, but performance drops significantly in actual wastewater. |
Performs equally well in both wastewater and clean water. This means the alpha value is approximately 1.0.
|
Discharged air bubbles rise slowly. Cannot uniformly churn the contents of the tank. Creates an anaerobic zone at the bottom of the tank. |
Discharged air bubbles rise exceptionally quickly, generating powerful circulating currents. No sludge accumulates on the tank floor. |
Lacks the ability to mix fluids, so cannot be used for improvements to chemical reactions at chemical plants. |
Possesses a powerful mixing function. Can be actively used to improve chemical reactions. |
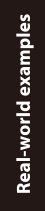 |
- Supplied to more than 4,000 factories. In the vast majority of cases, installation did not require draining or anchoring.
- Churning excess activated sludge in a holding tank at a chemical plant (SS: 20,000 mg/L). Maintenance-free for over 26 years.

- 12-hour on, 12-hour off intermittent aeration of wastewater containing high concentrations of calcium and magnesium (SS: 30,000 mg/L). Clog-free for over 18 years.

|
Limitations of conventional technology |
OHR technology |
Cannot generate sufficiently strong water currents, so sludge inevitably accumulates on the tank floor. |
Unique to the OHR AERATOR, violent spiral flows generate high negative pressures inside the unit, which churn up even heavy substances. |
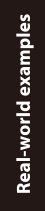 |
- No accumulation on the tank floor and no clogging for over 19 years, even in slurry containing more than 30% lime.

- One particular factory had been annually washing away up to 1.8 m of accumulated calcium carbonate. OHR AERATORs reduced sludge accumulation markedly.

- Accelerating Fenton’s reaction by churning and mixing as well as preventing deposits from accumulating on the tank floor.
|
Limitations of conventional technology |
OHR technology |
Performs bubbling with mechanical submersible aerators or porous air diffusers, both of which are inefficient and require excessive amounts of air. Cannot completely remove more tenacious substances. |
Possesses the ability to violently shake apart both gases and liquids, and to remove substances that remain in the liquid. Performs far more efficiently than the ostensibly more powerful mechanical aerators. (The OHR MIXER can also be used for inline processing.) |
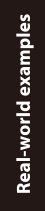 |
- Successfully removing VOCs that proved impossible to remove using mechanical submersible aerators.
- Removing VOCs from wastewater containing as much as 20,000–30,000 mg/L of slaked lime and VOCs. Before, porous air diffusers frequently clogged and required regular cleaning.; introducing OHR AERATORs rendered this cleaning entirely unnecessary and cut air usage by 40%.
- Aerating waste acid to remove sulfur dioxide gas.
|
Limitations of conventional technology |
OHR technology |
The common method for gas–liquid reaction involves injecting of gas into the liquid at the base of a bubble column reactor. Because these large bubbles are merely discharged, however, the majority of them escape into the atmosphere without making contact with or reacting with the liquid. This method is thus exceptionally inefficient. |
Simple bubbling cannot hold a candle to the OHR AERATOR, whose unique internal structures mix the gas and liquid together with both power and efficiency. (The OHR MIXER can also used for inline processing.) |
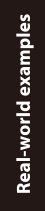 |
- Oxidizing SO₃ into SO₄ twice as efficiently as the previously-installed conventional air diffusers.
- Injecting exhaust gas that contains CO₂ into wastewater that contains slaked lime, in order to produce calcium carbonate. No clogging.
- Aerating and oxidizing iron dissolved in industrial water, in order to produce iron oxide for subsequent removal.
|