Mechanism diagram
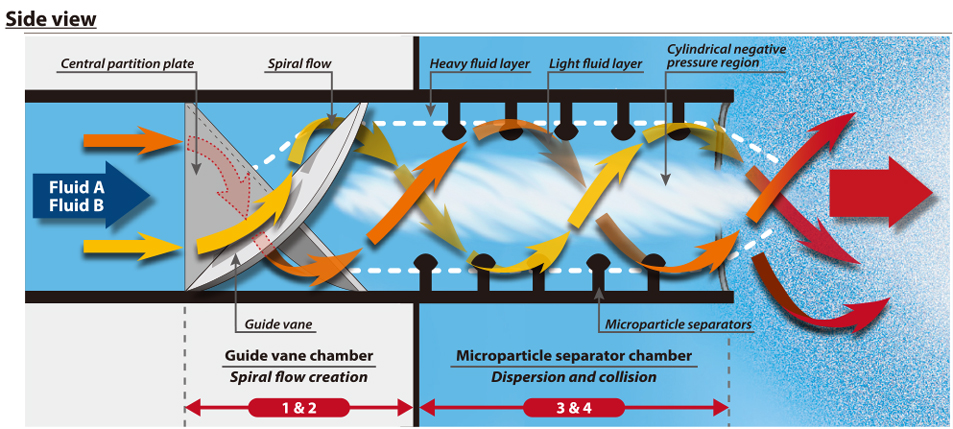
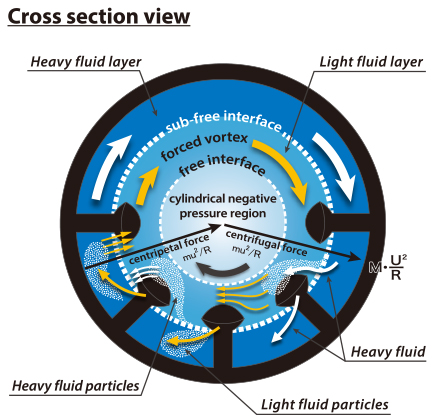
1. Create high-speed spiral flow
Fluids A and B flow into the reactor, where the guide vane converts them into a high-speed spiral flow and an extremely powerful centrifugal force.

2. Divide into layers
The difference in density between the two fluids causes the heavier fluid to move outwards and the lighter fluid to move inwards, during which time:
1. These randomly interdistributed fluids collide while being forcibly separated into layers, and
2. The difference in rotational speed causes turbulent eddies at the interface between them.

3. Break into fine particles
The microparticle separators instantaneously break down the two fluids into microparticles as the boundary layer separates over the caps of the separators.

4. Collide fine particles
The centrifugal and centripetal forces cause these microparticles, under a steep pressure gradient, to move in a ‘zig-zag’ fashion and collide with each other.
The entire process takes just 0.04 seconds to complete, with steps 3 and 4 repeating as many times as there are individual rings of separators, up until the end of the reactor.
OHR MIXER vs conventional static mixer
Conventional static mixer | OHR MIXER | |
---|---|---|
Intended use | For simple mixing and reactions | For difficult mixing and reactions |
Engineers worldwide are of the understanding that conventional static mixers can only be used for straightforward preliminary mixing. When first developed, these mixers were unquestionably innovative, and were expected to see practical applications in a variety of facilities. Gradually, however, it has become clear that they are useful only for pre-mixing. Should you need only the most basic mixing, please use this conventional type of inline mixer. |
The OHR MIXER can be used in extremely demanding situations: emulsification without emulsifier, uniform dispersion of trace additives, ozone treatment at volume, and more. It can also replace bulky equipment for chemical reactions. Please see the real-world examples linked below and the difference between the OHR MIXER and conventional inline mixers will become crystal clear. |
|
Structure and mixing principle | Multiple helical plates simply divide the fluids in two (1 becomes 2 becomes 4, and so on) |
Two unique structures: one divides the fluids into layers before the other breaks them down |
Conventional static mixers’ operate on the principle is that of division: internally-fixed helical plates repeatedly divide one fluid into two, two into four, and so on. This means that they inherently lack the ability to break down fluids into microparticles. In order to handle more difficult situations, multiple units have to be connected in series, which often results in large pressure losses and fluid not leaving the outlet. |
The OHR MIXER uses its two special internal structures — the guide vane and the unique mushroom-shaped separators inspired by research on aeroplane wings — to instantaneously break down fluids into microparticles using the principle of boundary layer separation, after which centrifugal and centripetal forces cause them to violently collide with each other. Its simplicity ensures that, unlike with conventional mixers, there is never a need to connect more than one unit in series. It does not force fluids through small holes or at high pressure; instead, it breaks down fluids using the principles of fluid dynamics. This makes the OHR MIXER a true original. |
|
Emulsification | Not possible without emulsifier even with a series of six mixers |
Possible without emulsifier at a low pump pressure of 0.3 MPa |
Because it fundamentally lacks a mixing function that could break down oil and water, it simply cannot emulsify, even if six are connected in series.
|
Despite their tendency to separate almost immediately, oil and water can be emulsified without emulsifier with a single pass through an OHR MIXER, all at an extremely low pump pressure of 0.3 MPa. In a magnificent demonstration of the OHR MIXER’s superior mixing ability, one of our customers managed to replace $200,000 of high-pressure emulsification equipment with a single $4,000 OHR MIXER. |
|
Particle size | Around 200 μm even with a series of six mixers |
0.5–3.0 μm in a single pass through a single unit |
Possesses very little ability to break down fluids, so can only perform basic mixing. |
Breaks down fluids into exceptionally fine particles in a single pass. |
|
Replacing reaction/ mixing equipment | Not possible | Possible |
Will only ever be capable of pre-mixing. | Conventional equipment is expensive, complex, bulky and high-pressure. Pivot to a single OHR MIXER and the change will be dramatic. “I want to expand abroad, but also downsize my equipment” “I want to save energy” “I want to create entirely new products” — no other static mixer can handle such envelope-pushing demands as these. |