The OHR method: ultra-efficient continuous deoxygenation as never before
There are many situations in which one may wish to perform deoxygenation in order to remove dissolved oxygen (DO) from liquid. In chemical plants, for example, oxygen dissolved in organic solvents poses an explosion risk during reaction processes, and dissolved oxygen can inhibit reactions.
A solution in cases like these is to steadily inject nitrogen gas (N2) into the liquid, raising the concentration of dissolved nitrogen beyond its natural state, which causes a corresponding decrease in dissolved oxygen. This phenomenon can be harnessed in order to lower DO, or reduce it almost to zero.
Conventional methods: bubbling large quantities of N2 gas over long periods of time
Deoxygenation by N2 gas is of the utmost difficulty
When the target deoxygenation rate is extremely high (e.g. 95%, 99%, 99.9% removal), conventional methods require a tremendously long time, such as a whole 24 hours. And worse still, because these methods involve filling a large tank with the target liquid and bubbling large quantities of nitrogen gas within it, batch processing is the only available option. Such methods take too long and cost too much.
This all leads to trouble in the form of soaring lead times, owing to the unexpectedly laborious deoxygenation process.
The OHR method can continuously reduce 10.0 mg/L of DO to 0.2 or lower
And makes it effortless to achieve.
Consider, for example, having to reduce a DO value of 10.0 mg/L down to 0.2 mg/L (=98% oxygen removal rate). Even in such an exceptionally difficult case as this, deoxygenation can be completed with continuous processing in a matter of seconds. Pressure increases, pressure decreases, deoxygenation agents — absolutely none of these are required.
For more details on the method, please contact us via the link below. We would be glad to share with you our diagrams, illustrations and independent test results.
The secret behind OHR’s high-efficiency deoxygenation
No other technology can achieve 130% N2 supersaturation with such ease
- In water at 20°C and 1 atm, air dissolves to a concentration of approximately 24 mg/L.
In other words, about 24 mg of air is dissolved in 1 L of water. Of this 24 mg, 15 mg is nitrogen plus a small quantity of argon, and the remaining 9 mg is oxygen.
(Other gases, such as carbon dioxide, neon and helium, are also present in negligible quantities.) - Now, this nitrogen and argon (hereafter simply "nitrogen") comprises about 79% of the air and dissolves into water, where it comprises 15 mg/L.
Suppose that, instead of air, extremely pure (close to 100%) nitrogen gas were injected into the water. To what value would the nitrogen concentration in the water increase? The answer: 19.0 mg/L (at 20°C and 1 atm).
This 19.0 mg/L is the limit of N2 dissolution in water, the saturation value. - From 15 mg/L to 19 mg/L is an increase in concentration of just 4 mg/L — with which observation it is now plain to see that expelling all of the dissolved oxygen at a single stroke is impossible. Methods that merely inject nitrogen gas therefore necessarily take a long time, e.g. 24 hours.
- How, then, can DO be removed from water efficiently? And moreover, removed continuously and instantaneously?
To achieve this, nitrogen gas must be dissolved, at a single stroke, into a state beyond normal saturation, called supersaturation. - The OHR method is able to achieve highly-efficient deoxygenation in just a few seconds because it increases the concentration of dissolved nitrogen in the water to 30% beyond its saturation point (i.e. 130%, taking saturation to be 100%), and does so at a single stroke.
The degree of oversaturation must be 130%. No lower level — 105%, 110%, etc — will suffice.
Without the technology to attain a markedly different level of supersaturation far beyond 19 mg/L (e.g. 25 mg/L), oxygen can never be "pushed out of the ring" at a single stroke, to borrow an analogy from sumo wrestling.
Please take a look at the graph on the right, which shows oxygen supersaturation measurements taken by Tokyo University of Marine Science and Technology.
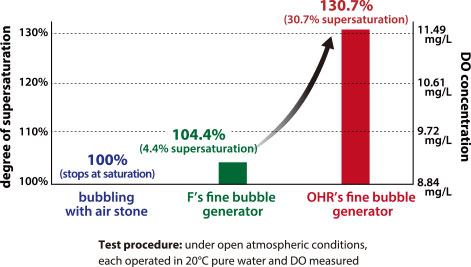
●Company F’s fine bubble generator reaches a supersaturation of 104.4%, that is, a mere 4.4% oversaturation.
●OHR’s fine bubble generator is able to reach 130% supersaturation (30% oversaturation) of oxygen. Naturally this means that is also able to reach 130% supersaturation of nitrogen.
These results are an example of how the many products marketed as "microbubble generators" actually differ greatly in their performance.
▶ Criteria for judging microbubble generators