[Solvent extraction] Mild, uniform mixing of oil and water
Mild mixing in solvent extraction (liquid–liquid extraction)
Owing to its exceptionally powerful fluid mixing capabilities, the OHR MIXER is most commonly used in situations that demand fine particles on the order of microns or nanometers. Here, however, we would like to introduce a slightly different use: mixing that is at once gentle and uniform.
The method known variously as solvent extraction (SX) or liquid–liquid extraction (LLE) allows target substances to be selectively extracted from liquid by harnessing the natural immiscibility of oil and water. It is principally used in fields such as metallurgy, edible oil refining and the extraction of flavorings.
In this article we will explain this process in simple terms, using the particular case of wet copper extraction as an example.
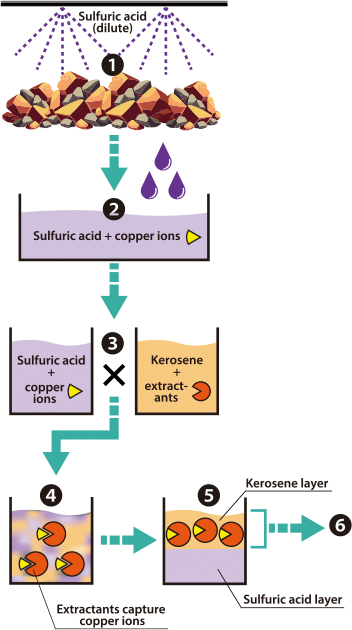
❶ Contact the copper ore or scrap with dilute sulfuric acid by spraying or soaking.
❷ Dissolve copper ions into the sulfuric acid.
❸ Use an agitator to mix this solution with kerosene (paraffin), dissolved into which are extractants that selectively capture only the copper ions.
❹ The copper ions dissolved in the sulfuric acid (the aqueous phase) are “caught” by the extractants and transfer into the kerosene (the oil phase).
❺ Allow to stand until the sulfuric acid (aqueous phase) and kerosene (oil phase) have separated into two layers.
❻ Send the kerosene (oil phase) on to the subsequent electrowinning process and obtain the copper.
Issues with solvent extraction
Solvent extraction is an inherently contradictory technique in that it seeks to create a harmonious combination of both mixing and separation. Steps ❸ and ❹ above proceed to transfer matter between the oil and aqueous phases by finely intermixing the two. Step ❺, however, proceeds to recover the target substance(s) by cleanly separating them.
Unless both mixing and separation are executed properly, yield will suffer. We will now break down how the OHR MIXER serves to balance these two opposing processes.
Although agitators are the most commonly used for oil–water mixing during the solvent extraction process, they are plagued by one issue: the very way they operate makes it very difficult to achieve proper contact between the two.
Agitators aim to contact and mix oil and water by rotating their blades, but the non-uniform distribution of the droplet sizes they produce results in the following issues:
- Uneven transfer of the target substance(s) between the two phases.
- During the separation process, after the oil and water have been contacted, any resulting overfine droplets will have poor separation efficiency, which negatively impacts yield.
- Droplets of oil that did not separate out linger in and contaminate the aqueous phase, making replacement and disposal costlier and more labor-intensive.
That is to say, the yield suffers if the oil droplet size is too large or too small.
We now turn our attention to agitators in operation. The different parts of the blades being different distances from the central shaft naturally results in a difference between relatively strongly-affected and relatively weakly-affected areas, which inevitably leads to a wide distribution of droplet sizes. Compounding the issue is the fact that there will always be a certain amount of leftover oil and liquid that has escaped without hitting the blades.
Firstly, the distribution of droplet sizes is broad, not sharp.
Secondly, a part always remains that escapes the blades.
Thus it may be said that agitators are fundamentally limited in two different senses.
Real-world example using the OHR MIXER
Here is an actual example of the OHR MIXER being used to extract organic solvents.
- The wastewater contains three types of organic solvent: toluene, cyclohexanone, and cyclohexanone oxime. All three were dissolved to a low concentration of around 200 ppm.
- The aim was to separate and extract the latter two (i.e. cyclohexanone and cyclohexanone oxime) from the wastewater by mixing in toluene. (This toluene was not pure — it had been recovered after earlier use in this extraction process.)
- The wastewater and toluene passed through the OHR MIXER at a pressure of just 0.03 MPa (about 1/10 the pressure of a typical household water supply).
- Both organic solvents were able to be recovered highly efficiently and we received glowing feedback from the company in question.
○ Cyclohexanone: extracted at a rate of 96.1% of the theoretical limit
○ Cyclohexanone oxime: extracted at a rate of 91.0% of the theoretical limit
This report is available upon request. Please contact us via the link below and we would be pleased to provide you with a copy.
▶ Contact us
Using the OHR MIXER for solvent extraction: the basic method
Using the OHR MIXER makes it possible to contact oil and water to within desired parameters. The key point is to feed the oil and water into the OHR MIXER at lower volume and pressure.
NB: it is strictly forbidden to feed oil and water at higher volume and pressure, as this will result in overfine particles.
It is important to conduct an advance test in order to determine the most appropriate flow rate and pressure, which will ensure smooth and clean separation after the oil and water have made proper contact. (This can be done by controlling the flow rate and pressure of the pump with an inverter.)
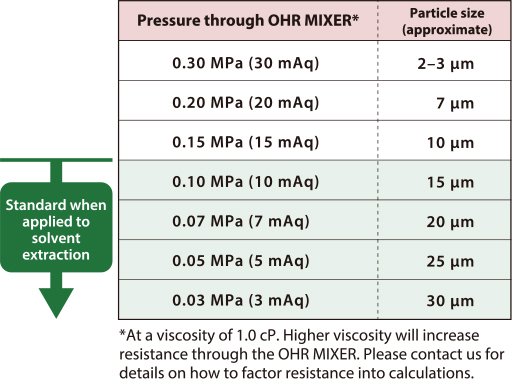
As a rough guide, a pressure of 0.10 MPa or below is typical.
Whether that pressure is ultimately 0.07, 0.05 or 0.03 MPa will be established via testing.
For reference, an OHR MIXER operating at a pressure of just 0.3 MPa emulsifies light fuel oil and water to a particle size of 2–3 microns. Moreover, this emulsification relies only on physical action forces, without the assistance of emulsifiers (chemical agents).
Please use the table on the right as a rough guide to resulting particle sizes at lower pressures.
The unmatched merits of the OHR MIXER
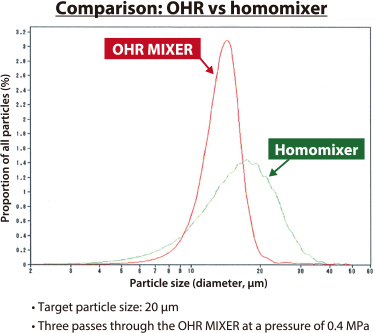
Here are five advantages of using the OHR MIXER for solvent extraction.
Advantage 1: Sharp distribution of droplet sizes.
The graph on the right is a comparison with a homomixer, which rotates blades at high speed within an outer casing.
Note that, although this particular test performed several passes through the OHR MIXER, in the majority of cases treatment is performed in a single pass.
Advantage 2: The entirety of the oil and water pumped into the OHR MIXER is broken down into fine particles.
Unlike with agitators, no amount of oil and water is left unprocessed.
Simply pump the fluids into the OHR MIXER, where the entirety will be instantaneously broken down and transformed into a mass of fine particles.
Please refer to the mechanism diagram below.
Advantage 3: The precision construction of the OHR MIXER’s internal structures ensures that, when fluid is passed through at a constant flow rate and pressure, the desired shear force is applied constantly and continuously.
Put another way, the OHR MIXER is able to achieve nothing short of the ideal oil–water mixing with exceptional consistency and stability.
Advantage 4: The OHR MIXER does not merely create droplets of uniform size and quality; its unique manner of operation enables it to complete the transfer from aqueous phase to oil phase in an instant.
The OHR MIXER comes equipped with a guide vane, a special internal structure that applies an extreme “wrench” to the mixture of fluids, creating a powerful centrifugal force that instantaneously divides it into two layers: an outward mass of heavier fluid particles and an inward mass of lighter fluid particles. These two particle masses then violently collide with each other. The collisions continue as these masses pass over the innovative microparticle separators.
Thus the transfer from aqueous phase to oil phase completes during this two-step collision process.
Suppose the OHR MIXER turned out to be best at creating droplets around 30 microns in size. It would not be the case that other equipment could attain the same rate of extraction by creating droplets of the same size; there is a qualitative difference at play here.
The correct understanding would be: “the strength of mixing that produces 30-micron droplets is precisely suited to cases using the OHR method for solvent extraction”.
Hence OHR technology is more likely to be able to achieve high-efficiency extraction, even if, for example, the particle size is larger than what has traditionally been considered optimal.
Advantage 5: Fluids take just 0.04 seconds to pass through the OHR MIXER. It can instantaneously mix oil and water even in enormous quantities (up to several thousand liters per minute), opening up possibilities for dramatic reductions in processing time.
Time previously allocated to agitator-based mixing can now be put to much better use in allowing the solution to stand for longer during the separation process.
Faster, more efficient separation of valuable resources
When it comes to recovering minor metals such as lithium, cobalt and nickel from waste lithium-ion batteries, solvent extraction may be said to be the most reliable technology currently available — and it is thought that this role will only become more important.
However, little improvement in yield can be expected as long as agitators are used for oil–water contact. This is down to the aforementioned fundamental limitations.
Should it turn out, for example, that a uniform droplet size of 30 microns is ideal both for mixing and for separation, the technology must be able to create that size of droplet with accuracy, and moreover must be capable of long-term stable operation.
We believe that the OHR MIXER is superlative in meeting these demands.