[Fine dispersion] OHR method for disintegration and dispersion of electrostatically-agglomerated fine powder
What exactly is disintegration?
Breaking up powder particles (metal, ceramic, resin, carbon etc) that have agglomerated in liquid
Because of cohesive forces (such as the van der Waals force and electrostatic forces) acting between them to keep them together, powder particles in liquid have a tendency to form large agglomerates over time, even if the powder has been thoroughly dispersed.
Spreading and redispersing these agglomerates requires the application of a so-called separation force that overcomes the cohesive forces. This process — applying a separation force to return the particles to their original size — is what we mean by “disintegration”.
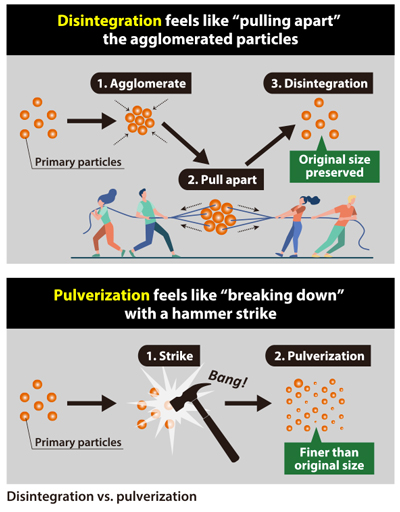
This is not to be confused with the similar term “pulverization”, which refers to the process of applying an impact force to a solid in order to crush it and make it smaller. This changes the primary particle size and therefore also the properties of the material (see illustration at right).
Applying sufficient separation force to overcome the cohesive forces in the
agglomerates is deceptively difficult and a perennial headache for engineers who work with slurry (=any mixture of solids and liquids).
With the OHR MIXER, however, disintegration is astonishingly easy. Allow us to explain how and why below.
Demerits of using pulverizers or agitators for disintegration
Power does not equate to pulverization ability
Many of the pulverizers available on the market are advertised as suitable for performing disintegration. Here are the most typical examples.
Ball mills and bead mills
These generate impact force by harnessing the energy of falling ceramic balls (known as the media), which are placed inside a rotating drum together with a slurry.
Hammer mills
These spin hammers at high speed; the heads of the hammers grind the slurry against the inside of the drum.
Disintegrating agglomerates using these types of equipment requires the application of mechanical impact force over a long period of time, and therefore has the following demerits. Please refer to the illustrations as you read.
- It changes the primary particle size. If this change occurs during processing, it will alter the properties of the material.
- The balls, beads, hammer heads etc wear down over time and contaminate the slurry.
- They are mainly used for batch processing, which takes considerable time. They are also bulky and power-hungry.
- With hammer mills in particular, the frictional heat alters the nature of the particles.
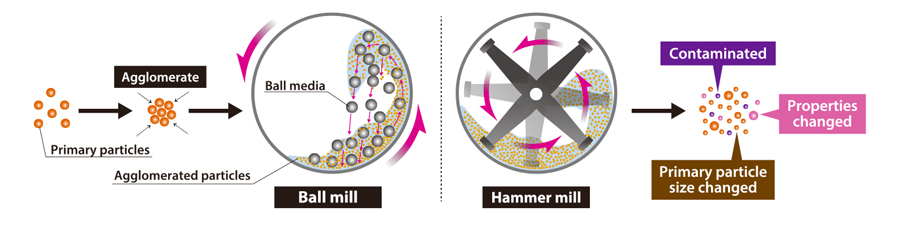
Although attempts have been made to use agitators for disintegration, in every case the target particle size proved unattainable even with long processing times. Attempting to use an agitator on fluids will result in so-called isolated mixing regions, where the fluid is at a standstill and no mixing occurs; however, this is not the sole reason for agitators’ inability to perform disintegration. It is also because the rapidly-rotating blades scarcely make contact with the agglomerates, and any contact that does occur is always an exceptionally weak impact.
Please see the video at right.
Note the addition of yellow resin (relative density close to 1.0) to represent the agglomerates.
On the practical side, as one customer reported, “We tried using an agitator, but it proved impossible, even with over a month of continued agitation.” This demonstrates a fundamental limit of agitators.
A successful case of disintegration with the OHR MIXER
Single pass, low pressure, excellent results
A chemical company had been unable to disintegrate carbon slurry that had formed agglomerates 5–10 mm in diameter. Disintegration remained impossible even with a variety of agitators and many hours of processing.
Despite this, the OHR MIXER was able to disintegrate and redisperse the agglomerated carbon exceptionally well in a single low-pressure pass (see treatment flow diagram below).
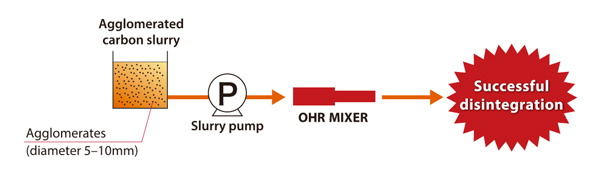
Moreover, the OHR MIXER requires just a few seconds for a single pass, and its use is not limited to carbon — we receive glowing feedback from our customers who also use it for metal powder, ceramic powder, resin powder, and all kinds of slurries. Please contact us for more details.
Contact us
How is the OHR MIXER able to disintegrate so well?
The entirety of the slurry receives a strong shear force
Pulverizers, disintegrators and agitators all work by applying impact force to slurry in a container; however, because some parts end up not receiving any of the impact force, processing will not be uniform.
One other reason for it being so difficult to make headway in disintegration is that by rapidly rotating solid objects in a slurry, everything in the vicinity of the agglomerates acts as a buffer, effectively shielding them from the impacts.
With the OHR MIXER, the entirety of the slurry passes through the mixer body, where it is uniformly impacted.
First, powerful centrifugal forces created by the guide vane forcibly separate the agglomerate and liquid components into two layers according to their relative densities, after which they zig-zag through and over multiple rings of microparticle separators that collide them together, producing extremely complex turbulent flow and applying shear forces.
The OHR MIXER can even replace high-pressure emulsifiers, a fact that clearly demonstrates the strength of the shear forces it produces.
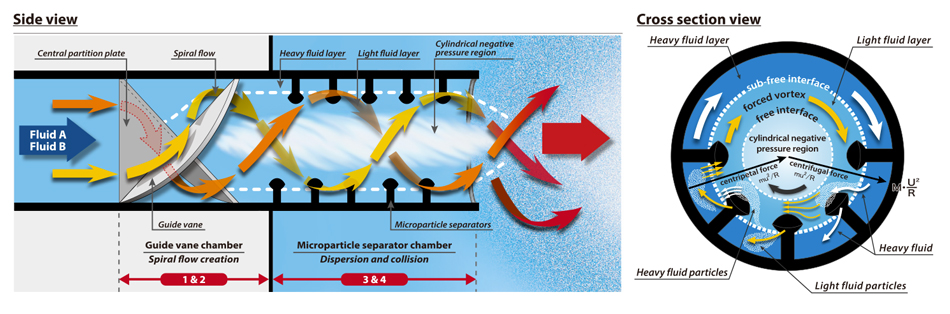
For more details about the mechanism, please see the link below.
Mechanism diagram
Although the OHR MIXER falls under the category of “inline mixers”, standard inline mixers are only able to generate very ‘simplistic’ flows (e.g. repeatedly dividing fluids in two using internal plates). Because agglomerates in slurry are surrounded by liquid, it is imperative to generate violent, complex flows that can cause repeated instantaneous collisions, lest the agglomerates move with the liquid and receive no impacts. Standard inline mixers cannot perform disintegration as the fleeting nature of the turbulent flow they produce means that the process ends prematurely, before the agglomerates can receive impacts.