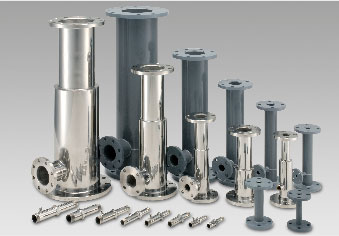
It is well-known that conventional static in-line mixers can only be used for pre-mixing and cannot complete chemical reactions by themselves. The far superior OHR MIXER, by contrast, can replace high-pressure emulsifiers, agitators, and reaction/pressure tanks.
In one particular case, a company was able to replace a $200,000 high-pressure emulsifier with a $3,800 OHR MIXER running at just 1% of the pressure.
Follow the link below to learn all about a selection of real-world cases that demonstrate our mixer’s capabilities.
Real-world cases
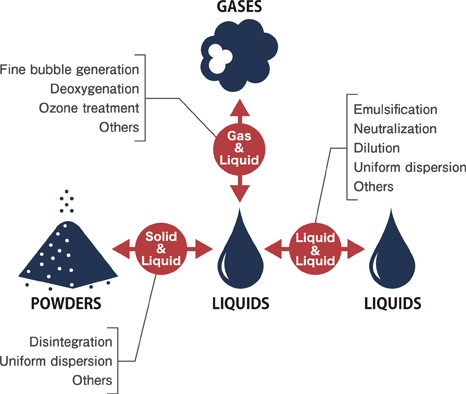
Conventional technology frequently combines bubbling with an agitator or pressure tank for gas–liquid reaction, and a high-pressure emulsifier or agitator for both liquid–liquid and solid–liquid mixing. However, all of these consume excessive amounts of power and time owing to low efficiency.
The core technology that is OHR vigorously mixes fluids (gases, liquids, powders) and breaks them down into ultrafine particles, hence it can be used for all kinds of purposes, depending on the pump with which it is combined. Typical examples of use are emulsification, disintegration, uniform dispersion, gas–liquid reaction, deoxygenation, and separation, in addition to a number of innovative and inventive examples. For more details, please watch the videos linked below, which focus on individual usages.
Seven use videos
Comparison
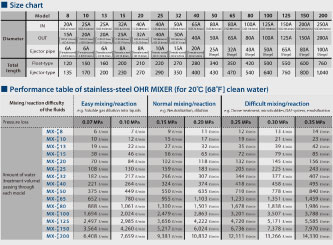
The OHR MIXER is available in thirty different models that each meet a variety of requirements, including treatment volume, permissible pressure loss, and your particular intended use. Everything from laboratory scale (10 L/min) to the largest scale (15,000 L/min) can be treated with the combination of one pipe and pump. Because the mechanism breaks down liquid–liquid, gas–liquid and solid–liquid solutions using fluid dynamic processes, performance is not impacted when a smaller model is scaled up to a larger one.
While our standard model is made of 304 (A2) stainless steel, we are able to manufacture the OHR MIXER using 316 or 316L (A4) stainless steel, nickel, titanium, PVC, Teflon or other materials upon request. For food and pharmaceutical manufacturing, we can also provide a special hygienic model.
Specifications
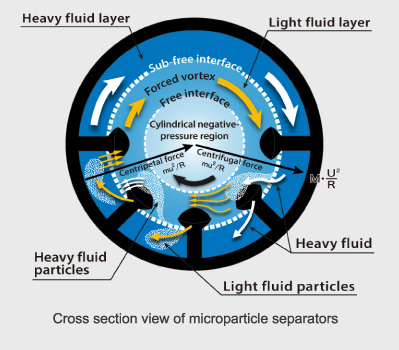
With ordinary static mixers, it is impossible to achieve the target mixing quality unless multiple are connected together in series, but this incurs large pressure losses and consumes large amounts of space.
By contrast, only one OHR MIXER is required per mixing line. The fluid is broken down in an instant (0.04 seconds) as it passes through, with the resulting fine particles undergoing repeated collisions due to the centrifugal and centripetal forces inside the OHR MIXER body.
This unique mechanism is realized via two kinds of special structure, the guide vane and the microparticle separators. The simple, elegant shapes make possible a level of performance that goes beyond the theoretical limits of fluid dynamics in spectacular fashion.
Mechanism
Technological philosophy
The real-world examples of issues that the OHR MIXER has successfully overcome and solved may seem unbelievable, but let us know your current technical issues and we would be more than happy to provide you with details of relevant success stories.
Feel free to contact us at your earliest convenience.
Contact / Inquiries
Checklist (PDF)