[Emulsion, fine dispersion, uniform mixing] OHR MIXER vs. conventional equipment
OHR MIXER vs. conventional equipment
A wide variety of agitators are used for emulsification, powder dispersion and uniform dispersion of trace components.
The most typical example is the homomixer, which shears liquid in a container using rapidly rotating blades, but high-pressure homogenizers are also frequently used; these collide liquids together by forcing them through narrow channels at high pressure. As is always mentioned when we receive inquiries about the OHR MIXER, perennial points of dissatisfaction with homogenizers include their performance, stability and maintenance.
In terms of performance, complaints range from poor mixing ability and excessive treatment time to low treatment capacity. The other complaints mention frequent breakdowns, and that maintenance is both costly and labor-intensive. Some complain that maintenance is difficult even in countries where maintenance support is readily available; and in areas where this support is lacking, using such complex equipment is out of the question.
Upgrading existing equipment to OHR MIXERs
In order to ascertain whether or not your homomixer or similar equipment can be replaced with OHR MIXERs, please contact us with details of the types and volumes of liquids you wish to mix, and we will provide you with details of the most suitable model of OHR MIXER as well as the required level of performance for the pump (please source this pump yourself). A special hygienic model intended for the manufacture of food and beverages is also available.
Now you are ready to test on site. In the majority of cases, results will match or exceed your existing equipment.
Once you have confirmed that the OHR MIXER performs adequately, there are no other barriers to replacement. Being a single pipe with fixed internal structures (i.e. there are no moving parts), it does not suffer breakdowns and does not require any maintenance. This means no additional costs or labor after installation, and stress-free operation day after day.
The OHR MIXER can also replace bead mills, ball mills and wet jet mills. Please note that, as the OHR MIXER does not have the ability to crush or pulverize solid materials, it cannot be used to break down primary particles. It is, however, exceptionally capable when it comes to disintegration and declumping. For detailed explanations, please see the following articles.
Instantly disintegrating and dispersing agglomerated fine powder in slurry
How to disperse clumped powder into liquid
Here is a real case of a chemical company that was unable to disintegrate a particular material until they tried the OHR MIXER.
- Their goal is to disintegrate carbon powder that has agglomerated to a size of 5–10 mm within a slurry.
- This powder proved impossible to disintegrate even after several hours of processing with many kinds of agitator.
- Despite this, the OHR MIXER achieved perfect disintegration in a single pass.
- The pump supplying the carbon slurry to the OHR MIXER operated at a pressure of just 0.3 MPa — as low as a typical domestic water supply.
How exactly does OHR MIXER match or outperform conventional mixing equipment?
Agitators are well-known for their tendency to create so-called Isolated Mixing Regions (IMRs), where comparatively little mixing takes place. This means that the particles in each region that cannot be broken down will remain unmixed, leading inevitably to a broad distribution of particle sizes.
The OHR MIXER, by contrast, creates no such unmixable regions. As fluids pass through the OHR MIXER, they are thoroughly broken down and transformed into fine fluid particles of uniform size, with the entire process completing at low pressure in just 0.04 seconds. Please take a look at the following mechanism diagram.
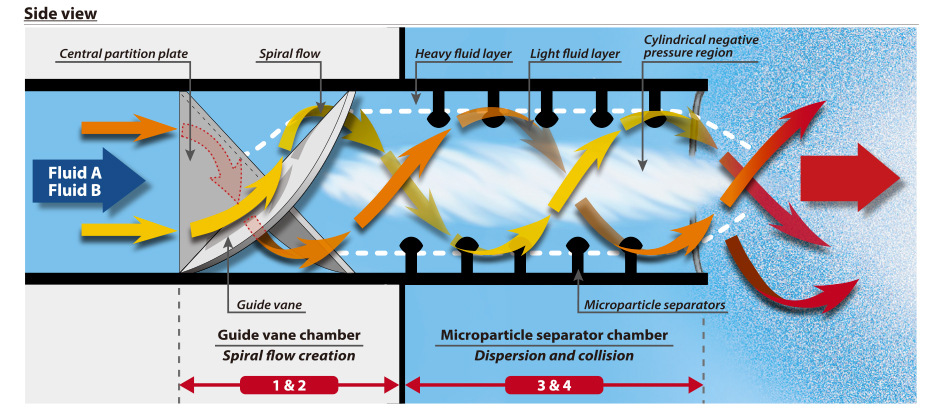
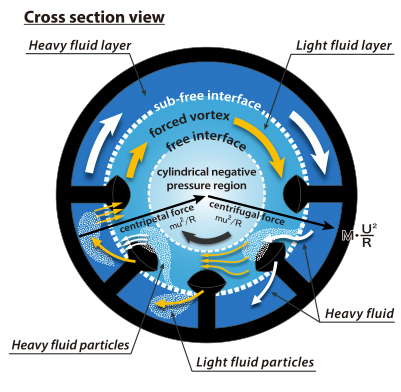
1. Create high-speed spiral flow
Fluids A and B flow into the reactor, where the guide vane converts them into a high-speed spiral flow and an extremely powerful centrifugal force.

2. Divide into layers
The difference in density between the two fluids causes the heavier fluid to move
outwards and the lighter fluid to move inwards, during which time:
1. These randomly interdistributed fluids collide while being forcibly separated into layers, and
2. The difference in rotational speed causes turbulent eddies at the interface between them.

3. Break into fine particles
The microparticle separators instantaneously break down the two fluids into microparticles as the boundary layer separates over the caps of the separators.

4. Collide fine particles
The centrifugal and centripetal forces cause these microparticles, under a steep
pressure gradient, to move in a ‘zig-zag’ fashion and collide with each other.
The entire process takes just 0.04 seconds to complete, with steps 3 and 4 repeating as many times as there are individual rings of separators, up until the end of the reactor.
OHR MIXER handles much higher volumes using much less electricity
Consider having to produce 1,000 liters of an emulsion or dispersion; in this case the OHR MIXER would require a pump rated at just 15 or 22 kW. Should a single pass be sufficient, this entire amount can be produced in a single minute.
By contrast, agitators, bead mills, wet jet mills, and high-pressure homogenizers all suffer from exceptionally low treatment capacity. For example, one of these products can process a maximum of 1,000 liters in 60 minutes and requires 75 kW of power, whereas the OHR MIXER can achieve this with a 0.75 kW pump — just one hundredth of the power — provided that the emulsion is not highly viscous. If combined with a 75 kW pump, the OHR MIXER can process 5,000 liters in a single minute.
Thus, compared to agitators, high-pressure homogenizers and similar equipment, the OHR MIXER is able to treat much larger volumes more quickly while using much less electricity.
By significantly increasing processing capacity, lead times can be slashed, affording a large amount of leeway in production.
The OHR MIXER is capable of dramatically improving production efficiency in plants and factories.
Whether or not your existing equipment can be replaced with an OHR MIXER naturally depends on your intended use and its particular conditions. Please let us know these details via the inquiry form or by email.